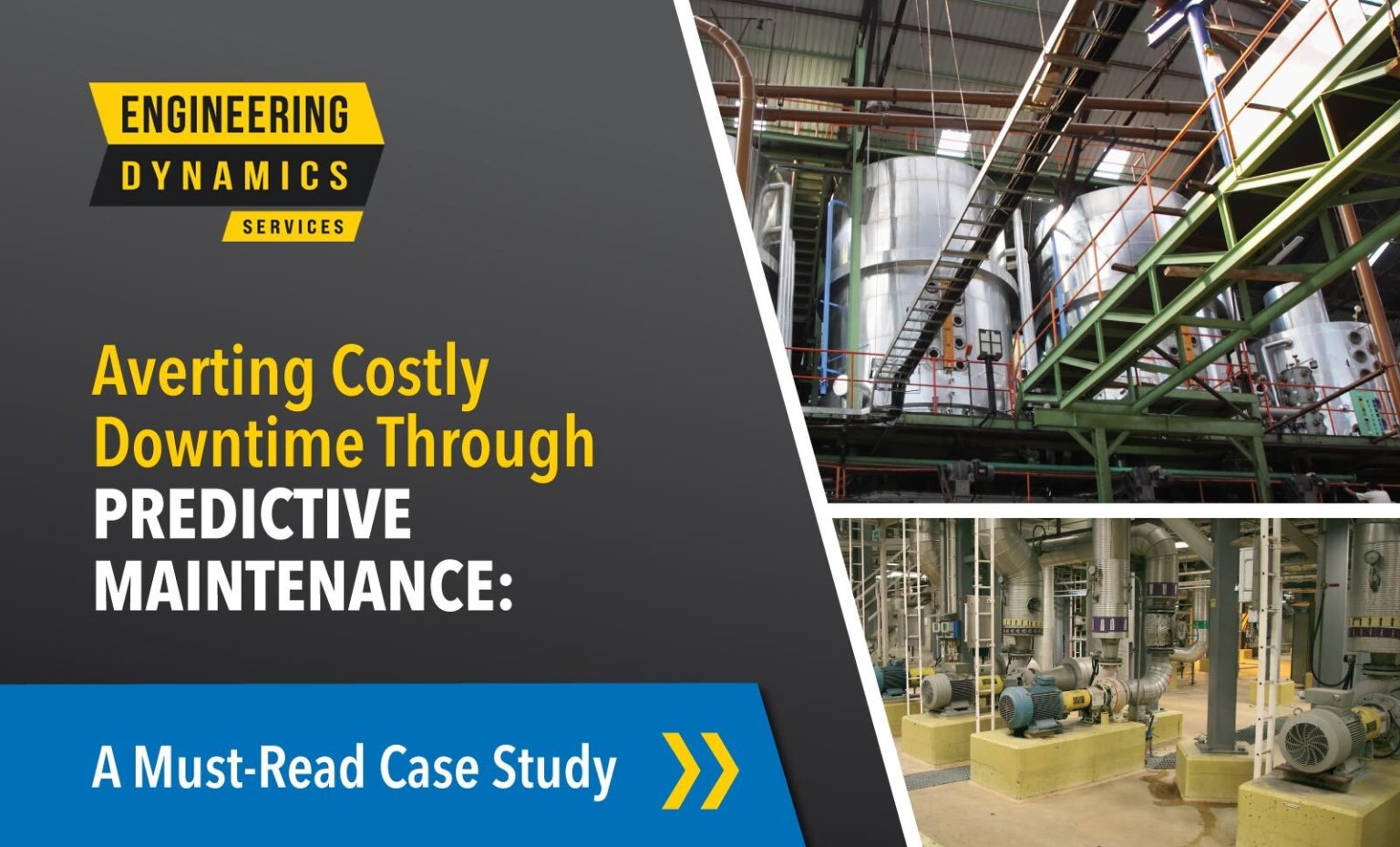
Vibration Monitoring Identifies Critical Bearing Issues on Boiler ID Fan Motor
Engineering Dynamics Services provides monthly comprehensive vibration analysis and predictive maintenance services to help our clients avoid unplanned downtime and optimise maintenance activities. A case study at one of our industrial plant customers highlights the benefits of utilising our services for critical equipment like boiler fans.
Introduction
During our routine monthly vibration monitoring in May of the year in question, we detected an upward vibration trend on both motor bearings of the Boiler 1 ID fan. Our report advised replacing both bearings if there was no improvement after greasing.
Findings
Almost a month later, our readings showed the drive end (DE) bearing was still running rough, while the vibration on the non-drive end (NDE) bearing as well as the fan bearings was increasing. We recommended replacing the DE bearing and inspecting the NDE bearing’s lubrication. The client reported a brand-new motor had been installed during that period.
In the middle of July, during our monthly vibration checks, the DE bearing vibration remained elevated, with a continued upward trend on the NDE bearing and both fan bearings. We reiterated our recommendations to replace the DE bearing and check the lubrication on the other bearings.
Recommendations
During our follow-up testing at the end of July, we found that the condition of the fan bearings was acceptable. The NDE bearing vibration had stabilised based on the latest readings but the DE motor bearing vibration continued its upward trend.
Our vibration analysis and documented trends clearly highlighted the need for timely corrective action on the motor bearings. We recommended that the client’s maintenance team promptly replace the drive-end (DE) motor bearing and continue monitoring the non-drive-end (NDE) bearing vibration levels.
Fortunately, the client acted swiftly on our recommendation and found that the old DE bearing was cracked, with failure imminent. By replacing the bearing just in time, they averted the high costs associated with repair and production downtime.
Conclusion
This case study exemplifies the value Engineering Dynamics Services brings through our vibration monitoring and analysis expertise. By tracking vibration trends over time and providing clear data-driven recommendations, we enabled the customer to schedule bearing replacements before catastrophic equipment failure.
Predictive maintenance based on machine reliability data allows for prioritising maintenance activities and optimising spending. Operating equipment until it fails, risks secondary damage, costly unplanned downtime, and health and safety issues. Our services help customers extend asset life, reduce maintenance costs, and improve overall plant reliability and uptime.
We encourage clients to take advantage of our vibration monitoring capabilities on critical rotating assets like fans, motors, pumps, and gearboxes. The potential rewards far outweigh the relatively low investment in predictive maintenance coupled with our other specialised services.
Motor NDE Bearing Horizontal
Motor DE Bearing Vertical
Motor DE Bearing Horizontal